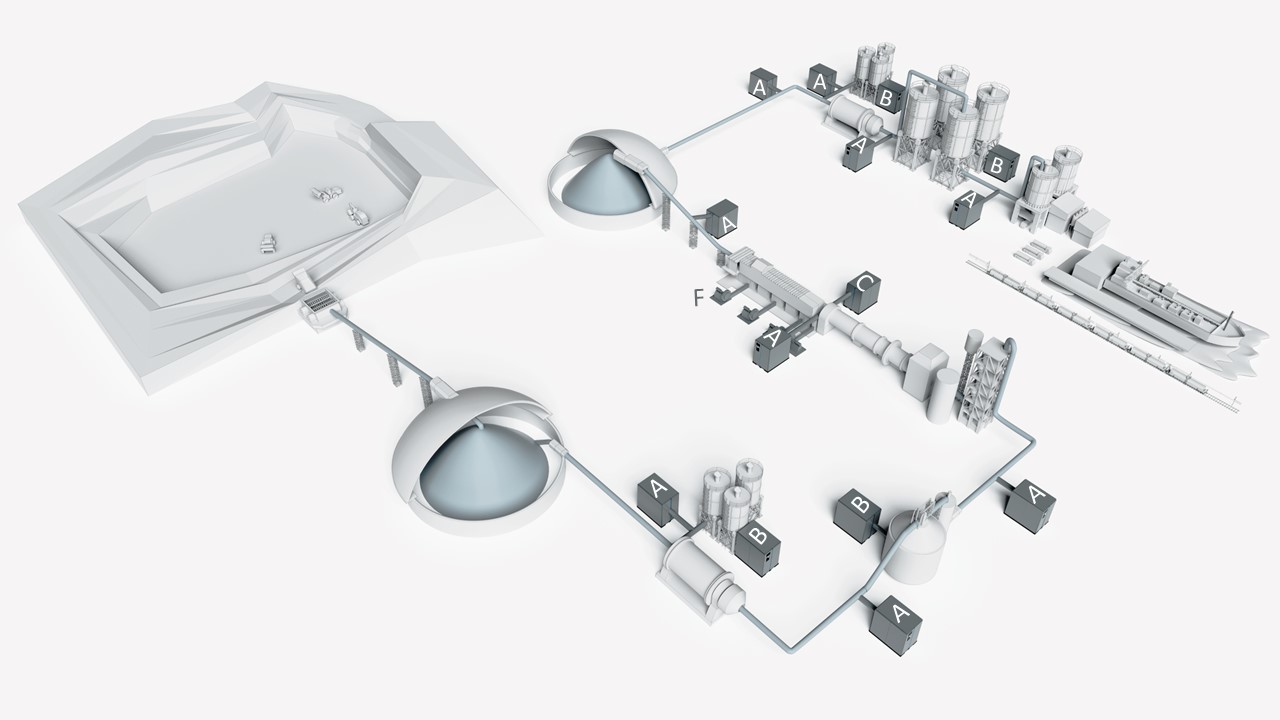
Quarry
The production of cement starts with the extraction of raw materials from a quarry. The main raw material is limestone, but it can also be clay, marl stone or chalk. The rocky materials have a heterogeneous composition and can have dimensions up to 1.8 meters. They are separated from the bedrock by blasting. After separation, they are collected by a crane into a truck so they can be transported to the crusher. At this stage, there is no or limited use of compressed air.
Crusher
Raw materials are the main materials required to produce cement. They are shipped by a truck from the quarry to a crusher, the first step of mechanical size reduction. This crusher reduces the materials to a size of 80 millimeters or less. At this stage there is no or limited use of compressed air.
Pre-homogenization
The goal is to have a homogeneous and stable cement composition at the end of the production process. In that way, it can be classified as, for example, Portland Cement (ASTM C150). However, the raw materials which are extracted from nature have a heterogeneous composition. To obtain this homogeneous cement composition several phases of homogenization are required. One of those phases it the pre-homogenization phase, in this phase of the production process, materials enter a large storage hall via the top and are layered in a specific sequence. This will ensure the raw materials are mixed and the mixture is homogeneous. After storing and increasing homogenization in the large storage hall, the materials are extracted at the bottom of the silo to be transported to the raw mill. Similar to step 1 and 2, at this stage there is no or limited use of compressed air.
Raw mill
The raw materials are transported from the pre-homogenization to the raw mill. Here, the materials are grinded into powder with particle sizes ranging from 20µm to 100µm. This can be done in a vertical or horizontal roller mill. The powder is known as raw meal or raw mix. The dust generated from this grinding process needs to be collected. This can be done in dust bag filters which are discontinuously cleaned by dust bag filter purge (4D). Once the raw materials are crushed into a powder, they are transported to the homogenization silo which can be done by pneumatic conveying (4A). At this stage, some additives can be added into the mill to limit the use of virgin materials. These materials can be sand, rock or sludge. These raw materials can be stored in vertical silos and transported by pneumatic conveying (5A) to the raw mill. Fluidization (5B) can be used to avoid blockages when extracting the materials from the silos.
Raw mill aggregates
The raw materials are transported from the pre-homogenization to the raw mill. Here, the materials are grinded into powder with particle sizes ranging from 20µm to 100µm. This can be done in a vertical or horizontal roller mill. The powder is known as raw meal or raw mix. The dust generated from this grinding process needs to be collected. This can be done in dust bag filters which are discontinuously cleaned by dust bag filter purge (4D). Once the raw materials are crushed into a powder, they are transported to the homogenization silo which can be done by pneumatic conveying (4A). At this stage, some additives can be added into the mill to limit the use of virgin materials. These materials can be sand, rock or sludge. These raw materials can be stored in vertical silos and transported by pneumatic conveying (5A) to the raw mill. Fluidization (5B) can be used to avoid blockages when extracting the materials from the silos.
Homogenization
The raw meal is pneumatically conveyed (5A) from the raw mill to the homogenization silo, where it is further homogenized. The raw meal enters the top of a typically vertical silo where it is initially stored in layers. These layers usually have different compositions. By applying a specific valve timing at the bottom of the silo, the layers are broken up. The more homogeneous raw meal is extracted at the bottom of the silo and pneumatically conveyed (6A) to the pre-heater. Fluidization (6B) can also be used here to avoid blockages during unloading of the silos.
Pre-heater
By going through the sequence of the pre-heater, kiln and cooler, raw meal is converted into clinker – small stones of a few centimeters or less.
The raw meal enters the top of the pre-heater. Air of the kiln is used to heat-up the raw meal in cyclones to a temperature of 850°C.
Kiln
A kiln can best be described as huge inclined and rotating tube where gravity transports the heated raw meal from the entrance to exit of the kiln. During transportation, the material is further heated to a temperature of 1450°C whereby it is sintered into clinker. Heating is done by a 2000°C flame located at the exit of the kiln. The flame is generated by using combustion air (8C) and a fuel, which can be conveyed to the burner (8A).
Cooler
In a final stage, cooling air (8F) is used to rapidly cool down the clinkers to a temperature of 100°. After they have been cooled down, the clinkers are pneumatically conveyed (9A) from the cooler to the storage hall.
Clinker storage
The clinker storage hall can be seen as a buffer stage in the continuous production process.
Delivering and extracting materials from the storage hall can be done via a pneumatic conveying (9A, 10A) installation.
Mill
The mill grinds the clinker, with some additives such as gypsum, fly-ash or slag into the end-product: cement (with particle sizes up to 100µm). The additives are typically stored in vertical silos and transported to the mill via a pneumatic conveying (11A) installation. To avoid blockages when unloading the silos, fluidization can be used (12B). Similar to the raw mill process, the dust generated during this production step is collected in dust bag filters which are cleaned by dust bag filter purge (11D). Transporting the cement from the mill to the storage halls is usually done through pneumatic conveying (12A).
Mill aggregates
The mill grinds the clinker, with some additives such as gypsum, fly-ash or slag into the end-product: cement (with particle sizes up to 100µm). The additives are typically stored in vertical silos and transported to the mill via a pneumatic conveying (11A) installation. To avoid blockages when unloading the silos, fluidization can be used (12B). Similar to the raw mill process, the dust generated during this production step is collected in dust bag filters which are cleaned by dust bag filter purge (11D). Transporting the cement from the mill to the storage halls is usually done through pneumatic conveying (12A).
Storage
The final product is stored in typical, large, vertical silos. These silos are filled from the top and later the material is loaded into trucks, ships or trains via the bottom of the silo. Here, fluidization (13B) can also be used to avoid that the material sticks to the bottom of the silo.
Loading
The final product is stored in typical, large, vertical silos. These silos are filled from the top and later the material is loaded into trucks, ships or trains via the bottom of the silo. Here, fluidization (13B) can also be used to avoid that the material sticks to the bottom of the silo.