H2Y compressors are designed to meet the specific challenges of hydrogen compression and storage. Along with maximum reliability, we prioritized safe handling and zero contamination, delivering the quality you need. Explore the highlights below to find out more.
Engineered for efficient hydrogen compression

H2Y
First view
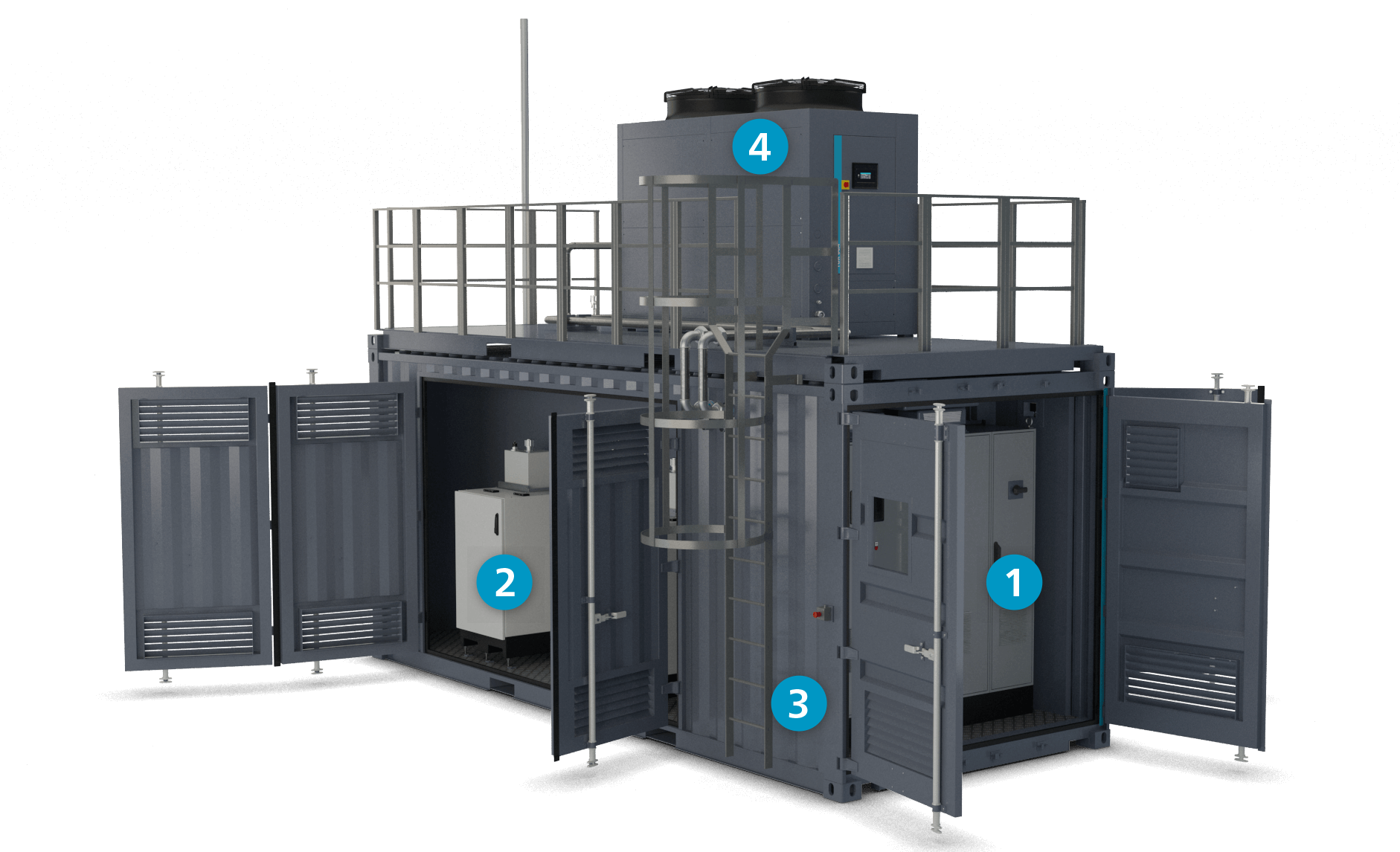
Second view
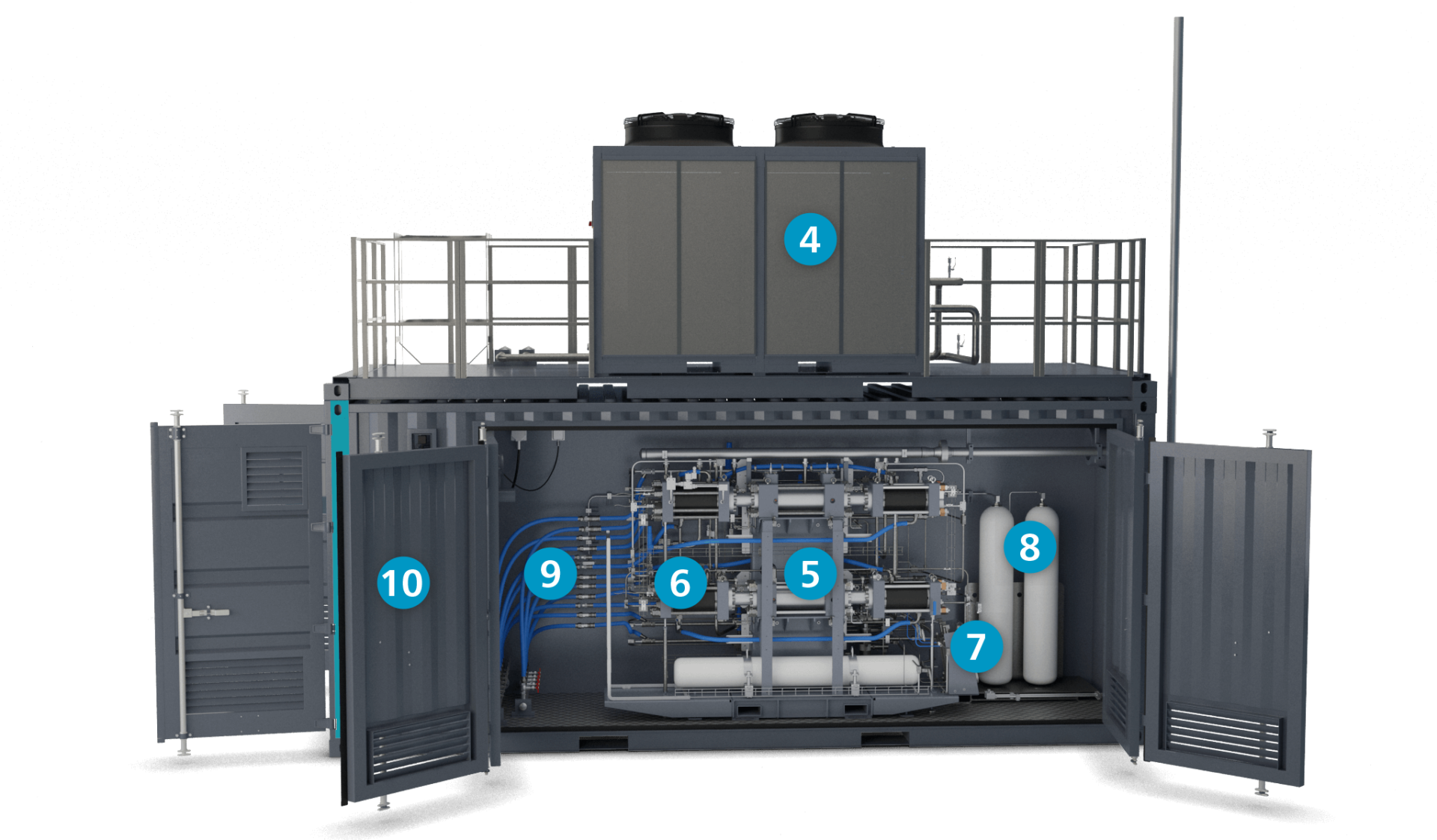
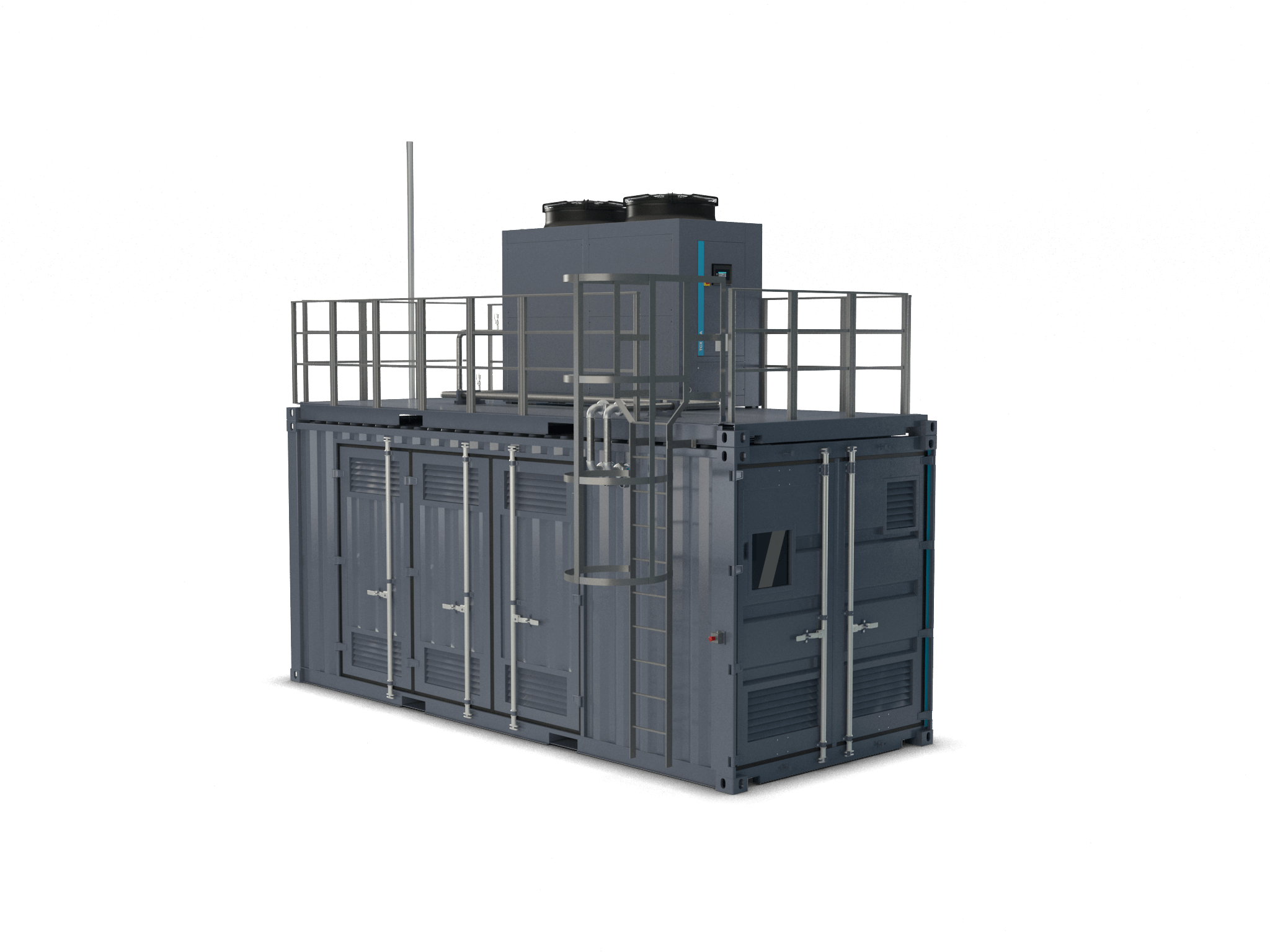
-
1
Control panel
-
2
Hydraulic power unit
-
3
Container
-
4
Atlas Copco TCX chiller
-
5
Core unit design for long service intervals
-
6
Distance piece
-
7
Leakage management system
-
8
Buffers
-
9
Piping & tubing
-
10
Safety in design
-
1
Control panel
• SIL level components (where needed) for managing safety
• Novel control philosophy
• In built UPS for fail safe operation
• Customer connectivity
• Fast acting PLC for reliable and efficient operation
• Variable inlet pressure and variable piston pump with AC logic to provide peak performance
-
2
Hydraulic power unit
• Atlas Copco own integration software to ensure energy efficiency and reliability
• Low power
• Low need of oil
• Low noise
-
3
Container
• Plug and Play solution
• Easy to transport and install
• In built safety system
• Exhaust system to ensure safe operation
• Integrated ladder for easy accessibility
• PLC mounted within container in safe area
-
4
Atlas Copco TCX chiller
-
5
Core unit design for long service intervals
• High quality cooling cylinder jackets
• Large compression chambers with ideal pressure ratio and RPM
• No blow-off during stop and restart
• Stage bypass system
• Extremely low vibration and pulsation
-
6
Distance piece
• 100% oil-free
• Reliable Atlas Copco piston rings for long life
• Long distance pieces ensure compression chambers are perfectly oil-free
• No risk hydrogen contamination
-
7
Leakage management system
• Automatic gas and oil chamber flushing system for manless operation
• Preventive maintenance through monitoring trends of Oil & Gas leakage
-
8
Buffers
• Inlet buffer to have steady inlet pressure readings from electrolyzers
• Available in ASME & PED versions
-
9
Piping & tubing
• All parts coming in contact with H2 are SS 316L or SS alloys
• Integrated tube in tube coolers
-
10
Safety in design
• 1x gas and flame detectors for explosion proof zone
• 2x extraction fan (explosion proof)
• Ergonomically located emergency shutdown buttons
• Appropriate grounding between control panel and compressor