Oil and air flows: your step-by-step guide
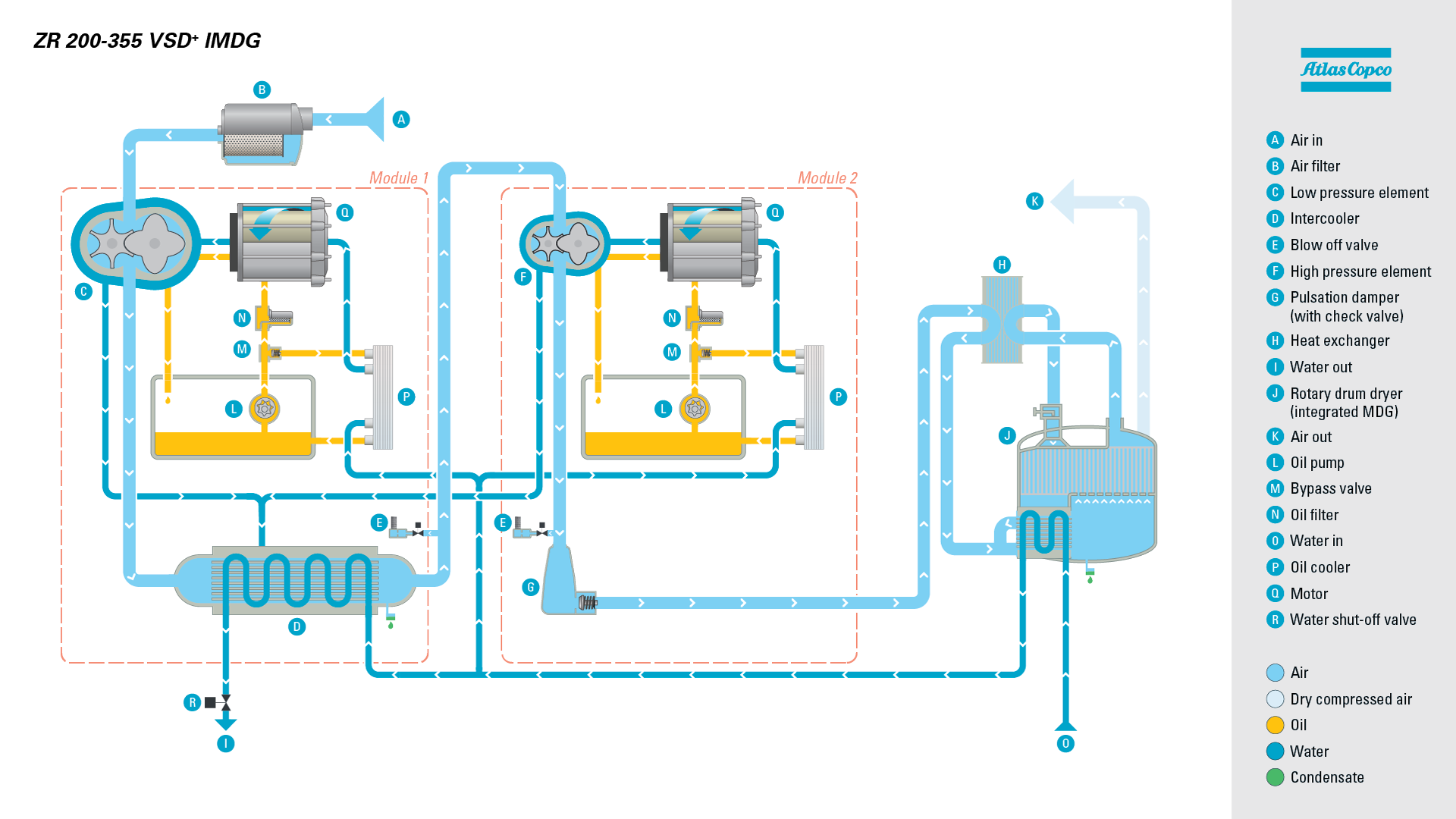
Filtration & compression
The air is drawn into the compressor through the inlet filter where the air is cleaned. It then continues to the first compression stage where the air is compressed to an intermediate pressure.
Cooling & second compression
After the first compression, the air is cooled down in the intercooler. Once the air is cooled down, it passes through a moisture separation system before entering the high-pressure stage. In the high-pressure stage, the pressure is brough to its final pressure.
Exchanging heat & cooling
The hot wet compressed air at the outlet of the high-pressure stage goes through the pulsation damper with integrated check valve to the heat exchanger. Here it transfers the heat to the integrated dryer used further in the process. The air continues to the aftercooler where it is cooled down and the poisture gets separated and drained.
Integrated dryer
The cooled wet compressed air is now mixed with 40% of the cooled regeneration air and enters the dryer. The dry compressed air with guaranteed dew point is now ready for use in your application.
Heat exchanger
40% of the dry air goes into the heat exchanger, where it picks up the heat from the incoming hot wet compressed air. This dry and hot regeneration air enters the regeneration section of the drum, which passes through the regeneration cooler where it is cooled down and moisture is separated and drained. Afterwards it is mixed with the incoming cooled wet compressed air.
Oil
The yellow lines represent the oil flow of the compressor. Oil is pumped from the reservoir through a high efficiency filter to provide clean, cooled oil to the gears for lubrication. Afterwards the oil flows back into the reservoir. There is also a bypass valve that allows the oil to flow to the oil cooler, so the optimal temperature is guaranteed, increasing efficiency and durability of the components.
Water
The dark blue lines represent the water flow. Cooling water is brought into the cycle and splits towards both modules and the dryer. First of all, the cooling water is directed to the integrated dryer. Secondly, the water goes to both the inter- and aftercooler te reduce the temperatie of the compressed air. Lastly, the water splits to the oil coolers to reduce the temperature of the oil. It then passes through the jackets of the motor and elements to guarantee an optimal temperature. The water continues back to the cooler and is directed further to the water outlet.
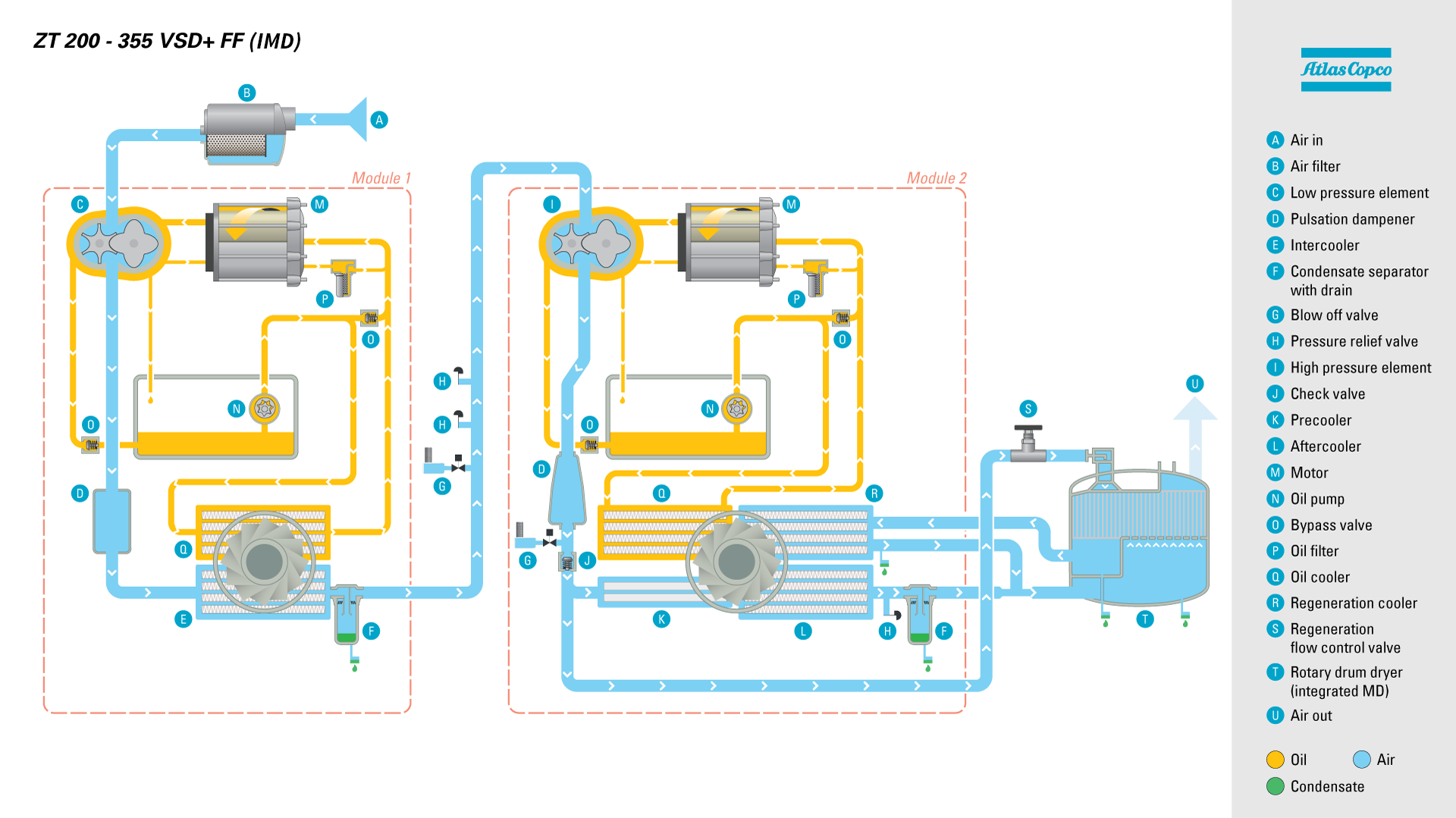
Filtration & 1st stage compression
The air is drawn into the compressor through the inlet filter where it is cleaned. Then, it continues to the first compression stage. There, it is compressed to an intermediate pressure.
Cooling – 1st stage
The compressed air flows through the pulsation dampener to the intercooler. It is cooled down there. After the intercooler, it passes through a moisture separation system with automated drains to remove the condensate before entering the high-pressure stage. The blow off valve and two pressure relief valves located after the moisture separator. They safeguard the system from accidents.
2nd stage compression
After the intercooler, the air is compressed in the high-pressure stage to the final pressure. The high pressure compressed air then flows through pulsation dampener and check valve.
Cooling – 2nd stage
For a machine without integrated dryer, compressed air flows through precooler and aftercooler where it is cooled. Then, it moves to the outlet of the machine.
For a machine with an integrated dryer, the compressor air flow splits into two parts. Approximately 60% of the first flow goes through precooler and aftercooler where it is cooled down. There, moisture is separated and evacuated. The second part goes directly to the regeneration area of the heat of compression MD dryer.
Integrated dryer
The flow to regeneration side of the dryer can be controlled through the flow control valve present in the circuit. In the regeneration area of the dryer, the hot air regenerates the adsorption drum after which it passes through the regeneration cooler where it is cooled down and moisture is separated and evacuated. The cold air coming from the regeneration section is then mixed with the cold air from the aftercooler in the nozzle before passing through the drying section of the adsorption drum where the moisture is removed. Dry air leaves the compressor through the outlet connection flange.
Oil
The yellow flow is the oil path within the compressor where the oil pump sucks oil from the oil sump and pumps it through the oil cooler. The cooled oil from oil cooler splits into two flows. The first oil flow line is directed towards motor jacket and element jacket to remove heat from both the motors and elements. The second flow line moves through a high efficiency filter to give cool and clean oil to the gears for lubrication. Then, the oil flows back to the oil sump. The oil bypass valves present in the oil circuit protect the oil filter from high oil pressure and make sure sufficient oil pressure is maintained in the oil circuit.