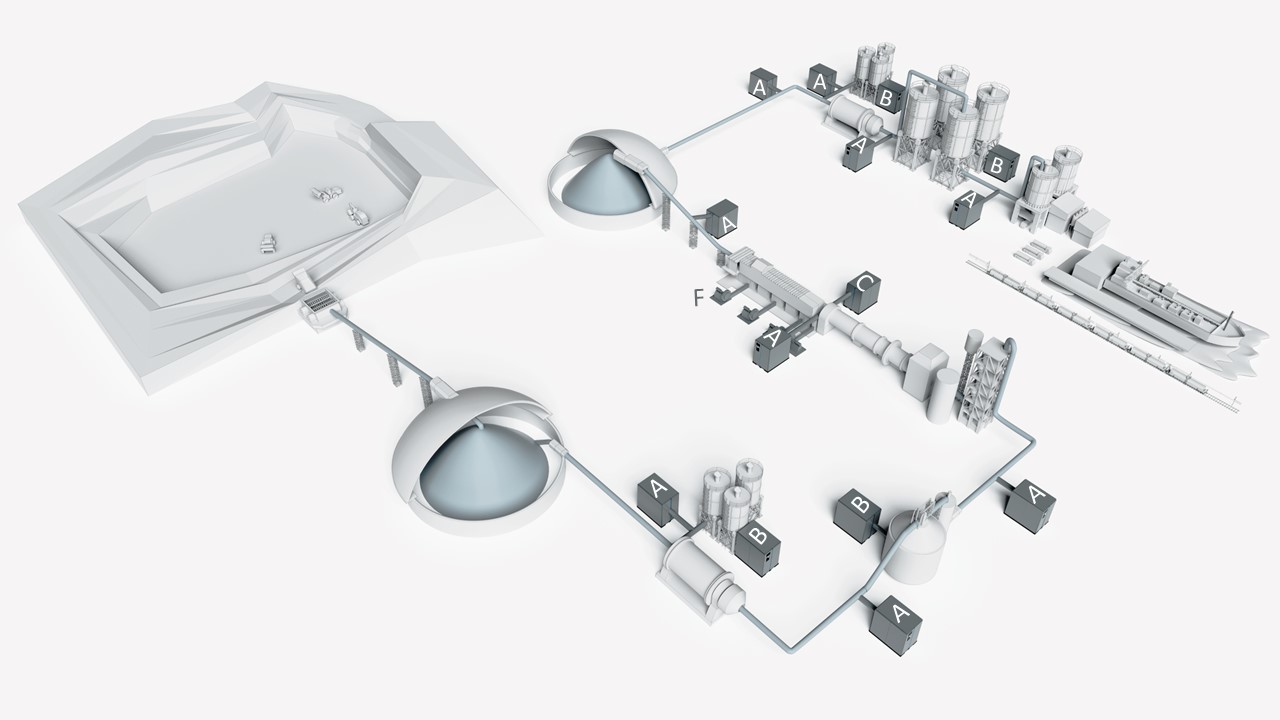
Quarry
Pierwszym etapem produkcji cementu jest wydobycie surowców w kamieniołomie. Podstawowym surowcem jest wapień, ale może to być również glina, margiel lub kreda. Wydobywany materiał skalny jest niejednolityi ma wielkość do 1,8 m. Oddziela się go od skały macierzystej metodą strzałową. Oddzielony materiał ładuje się na wozidła, które transportują go do łamacza. Na tym etapie nie używa się sprężonego powietrza lub wykorzystuje się je w ograniczonym zakresie.
Crusher
Najważniejszym materiałem potrzebnym do produkcji cementu są surowce. Wozidła przewożą surowce z kamieniołomu do łamacza, który odpowiada za ich wstępne rozdrobnienie. Łamacz rozdrabnia materiał na fragmenty o wielkości 80 mm lub mniejszej. Na tym etapie nie używa się sprężonego powietrza lub wykorzystuje się je w ograniczonym zakresie.
Pre-homogenization
Gotowy cement musi być jednorodną i stabilną mieszaniną. To warunek spełnienia wymogów — np. normy ASTM C150 w przypadku cementu portlandzkiego. Jednak surowce wydobywane w kamieniołomach mają budowę niejednolitą. W celu uzyskania jednorodnej mieszaniny trzeba zrealizowaćkilka faz homogenizacji. Jedną z nich jest faza homogenizacji wstępnej, w której materiał trafia od góry do dużej hali składowania i jest w niej układany w warstwy w określonej kolejności. Zapewnia to wymieszanie surowców i uzyskanie jednorodnej mieszaniny. Materiał zmagazynowany i wstępnie wymieszany w hali pobiera się od spodu silosu i transportuje do młyna. Podobnie jak na etapie 1. i 2., na tym etapie nie używa się sprężonego powietrza lub wykorzystuje się je w ograniczonym zakresie.
Raw mill
Po zakończeniu homogenizacji wstępnej surowce trafiają do młyna. Mielone są tu na proszek, którego cząstki mają wielkość od 20 do 100 µm. Do rozdrabniania używa się pionowego lub poziomegomłyna walcowego. Sproszkowany materiał to tzw. mączka surowcowa. W procesie mielenia powstaje pył. Wychwytuje się go z użyciem filtrów workowych, które są okresowo opróżniane przy użyciu nadmuchu powietrza(4D). Sproszkowane surowce trafiają do silosu do homogenizacji, np. za pośrednictwem pneumatycznych systemów transportowych(4A). Na tym etapie można zastosować niektóre dodatki, takie jak piasek, kamień lub szlam, aby ograniczyć wykorzystanie materiałów pierwotnych. Surowce można składować w silosach pionowych, z których za pośrednictwem pneumatycznych systemów transportowych(5A) trafiają one do młyna do surowca. W uniknięciu zatorów podczas wydobywania materiału z silosówmoże pomóc fluidyzacja (5B).
Raw mill aggregates
Po zakończeniu homogenizacji wstępnej surowce trafiają do młyna. Mielone są tu na proszek, którego cząstki mają wielkość od 20 do 100 µm. Do rozdrabniania używa się pionowego lub poziomegomłyna walcowego. Sproszkowany materiał to tzw. mączka surowcowa. W procesie mielenia powstaje pył. Wychwytuje się go z użyciem filtrów workowych, które są okresowo opróżniane przy użyciu nadmuchu powietrza(4D). Sproszkowane surowce trafiają do silosu do homogenizacji, np. za pośrednictwem pneumatycznych systemów transportowych(4A). Na tym etapie można zastosować niektóre dodatki, takie jak piasek, kamień lub szlam, aby ograniczyć wykorzystanie materiałów pierwotnych. Surowce można składować w silosach pionowych, z których za pośrednictwem pneumatycznych systemów transportowych(5A) trafiają one do młyna do surowca. W uniknięciu zatorów podczas wydobywania materiału z silosówmoże pomóc fluidyzacja (5B).
Homogenization
Pneumatyczne systemy transportowe (5A) przenoszą mączkę surowcowąz młyna do silosu do homogenizacji,w którym odbywa się dalsza homogenizacja. Mączka trafia do górnej części silosu (zazwyczaj pionowego), gdzie jest wstępnie układana w warstwy. Warstwy te mają zwykle odmienny skład. Odpowiednie sterowanie zaworami w dolnej części silosu powoduje rozbicie warstw. Od spodu silosu pobiera się mączkę, teraz bardziej jednorodną, i przenosi się ją za pomocą pneumatycznych systemów transportowych(6A) do podgrzewacza wstępnego. W celu uniknięcia zatorów podczas wydobywania materiału z silosów stosowana jest fluidyzacja (6B).
Pre-heater
Mączka surowcowa trafia kolejno do podgrzewacza wstępnego, pieca i chłodnika, dzięki czemu zmienia się w klinkier — drobne kamienie o wielkości do kilku centymetrów.
Mączka przenoszona jest na górę podgrzewacza wstępnego. Gorące powietrze z pieca nagrzewa mączkę w cyklonowych wymiennikach ciepła do 850°C.
Kiln
Piec tow uproszczeniu ogromna nachylona, obracająca się rura,w której podgrzewana mączka przemieszcza się do strefy wylotowej pod wpływem grawitacji. Podczas transportu materiał jest dalej podgrzewany, do temperatury 1450°C. Dzięki temu jest on spiekany i powstaje klinkier. Do podgrzewania używa się płomienia o temperaturze 2000°C i palnika usytuowanego na wylocie pieca. Płomień wytwarza się przy użyciu powietrza spalania(8C) i paliwa doprowadzanegodo palnika (8A).
Cooler
Na koniec używa się powietrza chłodzącego(8F), aby szybko schłodzić klinkier do temperatury 100 stopni. Schłodzony klinkier przenosi się za pomocą pneumatycznych systemów transportowych (9A) z chłodnika do hali składowania.
Clinker storage
Hala składowania to miejsce tymczasowego magazynowania klinkieru w ciągłym procesie produkcji.
Doprowadzanie i odprowadzanie materiału może odbywać się z użyciem pneumatycznych systemów transportowych(9A, 10A).
Mill
Młyn rozdrabniaklinkier i wzbogaca goo dodatki, takie jak gips, popiół lotny lub żużel. W ten sposób powstaje produkt końcowy — cement.Cząstki mają wielkość do 100 µm. Dodatki zazwyczaj przechowuje się w silosach pionowych i transportuje do młyna za pośrednictwem pneumatycznych systemów transportowych(11A) . W uniknięciu zatorów podczas opróżniania silosów może pomóc fluidyzacja (12B). Podobnie jak w młynie do surowca powstający pył wychwytują filtry workowe, opróżniane z użyciem nadmuchu powietrza(11D). Transport cementu z młyna do hal składowania odbywa się zazwyczaj z wykorzystaniem pneumatycznych systemów transportowych(12A).
Mill aggregates
Młyn rozdrabniaklinkier i wzbogaca goo dodatki, takie jak gips, popiół lotny lub żużel. W ten sposób powstaje produkt końcowy — cement.Cząstki mają wielkość do 100 µm. Dodatki zazwyczaj przechowuje się w silosach pionowych i transportuje do młyna za pośrednictwem pneumatycznych systemów transportowych(11A) . W uniknięciu zatorów podczas opróżniania silosów może pomóc fluidyzacja (12B). Podobnie jak w młynie do surowca powstający pył wychwytują filtry workowe, opróżniane z użyciem nadmuchu powietrza(11D). Transport cementu z młyna do hal składowania odbywa się zazwyczaj z wykorzystaniem pneumatycznych systemów transportowych(12A).
Storage
Produkt końcowy zwykle składuje sięw dużych silosach pionowych. Silosy wypełnia się od góry, a materiał pobierany w ich dolnej części ładuje się na ciężarówki, statki lub wagony. Aby materiał nie przywierał do dna silosu, można użyć fluidyzacji(13B).
Loading
Produkt końcowy zwykle składuje sięw dużych silosach pionowych. Silosy wypełnia się od góry, a materiał pobierany w ich dolnej części ładuje się na ciężarówki, statki lub wagony. Aby materiał nie przywierał do dna silosu, można użyć fluidyzacji(13B).